Resurfacing Pads: Selection, Application & Maintenance Guide
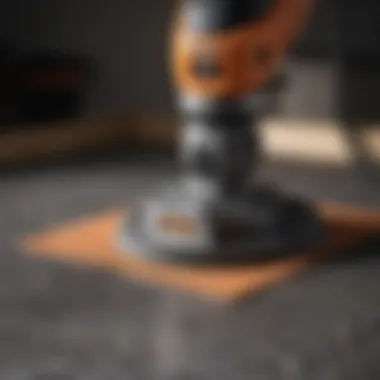
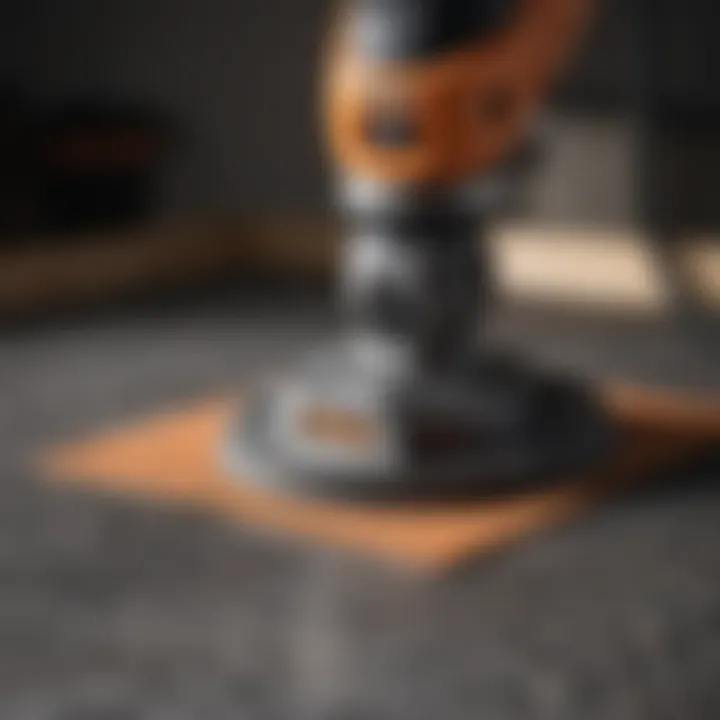
Intro
Resurfacing pads are essential tools used in various fields such as automotive repair, woodworking, and construction. Understanding their selection, application, and maintenance can significantly impact the quality of the work performed. In this guide, we will explore the importance of resurfacing pads, the criteria for choosing the right type, and how to effectively use and maintain them. By familiarizing yourself with these aspects, you will be better equipped to enhance your projects and ensure optimal results.
Selecting Resurfacing Pads
Choosing the right resurfacing pad is vital for achieving desired outcomes. Different projects require specific pads based on their material and design. Here are some factors to consider:
- Material: Resurfacing pads come in various materials, each suited for particular jobs. Nylon and polyester pads are common in woodworking, while foam and urethane pads are preferable for automotive applications.
- Coarseness: The grit size determines how aggressive the pad will be. Finer pads are useful for finishing, while coarser pads are better for initial resurfacing efforts.
- Type: Various types of resurfacing pads exist, including velcro-backed and non-woven pads. The choice depends on the tools available and the tasks at hand.
By evaluating these criteria, one can select the pad that best suits the project.
Application Techniques
Using resurfacing pads correctly is crucial for effectiveness. Here are some important techniques:
- Prepare the Surface: Ensure the surface is clean and free of debris. This helps in achieving smooth results.
- Appropriate Tool: Use the right tool for the pad. For example, rotary tools are ideal for small tasks, while floor sanders are better for larger areas.
- Control Pressure: Apply consistent and moderate pressure when using the pad. Too much pressure can damage the surface or the pad itself.
- Technique: Move the tool in a controlled manner, avoiding pauses that may cause uneven surfaces.
These practices help in maximizing pad performance.
Maintenance of Resurfacing Pads
Maintaining resurfacing pads ensures their longevity and efficiency. Here are some tips:
- Cleaning: Regularly clean pads after use. Dust and debris can clog the surface, reducing effectiveness.
- Storage: Store pads in a cool, dry place away from direct sunlight to prevent deterioration.
- Inspection: Periodically check pads for wear and tear. Replace them once they start to lose effectiveness.
Following these maintenance steps can prolong the life of resurfacing pads and sustain optimal performance.
Proper selection, application, and maintenance of resurfacing pads are essential to achieving professional results in any project.
Epilogue
Understanding resurfacing pads is important for anyone involved in tasks that require surface preparation. By selecting the right pad, applying it effectively, and maintaining it properly, users can enhance their work quality significantly. This guide serves as a foundation for making informed decisions about resurfacing pads in automotive, woodworking, and construction projects.
Preamble to Resurfacing Pads
Resurfacing pads serve a crucial role in various fields, from automotive repairs to woodworking and construction projects. Understanding their importance can greatly enhance the effectiveness of any undertaking. Improperly selected or used resurfacing pads can lead to poor results or even damage to the materials being worked on. Therefore, grasping the nuances of these tools can ensure success in achieving desired outcomes.
Definition and Purpose
Resurfacing pads are tools designed to refine and prepare surfaces for further work. Their primary function is to remove imperfections and create a smooth finish. Different types of pads cater to specific surface materials and applications. For example, diamond resurfacing pads are commonly used for grinding tougher materials like concrete, while alumina oxide pads are effective on softer substrates, such as wood.
The purpose of using resurfacing pads extends beyond mere aesthetics. They play an essential role in ensuring the longevity and durability of the surfaces being treated. A well-prepared surface increases adhesive bonding in various applications, including paint and coatings. Additionally, they help to maintain machinery, ensuring that parts work efficiently and extend overall equipment life.
Common Applications
Resurfacing pads find diverse applications across several industries. In automotive sectors, they are crucial for brake disc resurfacing. Here, accuracy is vital, as any imperfections can cause inefficiencies in vehicle performance. In woodworking, they assist in surface preparation, ensuring that wood is smoothed out before finishing.
In construction, these pads are invaluable for tasks such as floor leveling and tile preparation. Each application demands a precise pad type and grit size, making selection a key factor in achieving effective results.
By understanding the definition and broad applications of resurfacing pads, users can better appreciate their role and make informed choices in their use.
Types of Resurfacing Pads
Understanding the types of resurfacing pads is essential for anyone involved in automotive, woodworking, or construction. Each type of pad offers distinct benefits and is suited for specific applications. By recognizing these differences, users can optimize their projects, ensuring better results and more efficient use of resources.
Diamond Resurfacing Pads
Diamond resurfacing pads are renowned for their durability and effectiveness. They feature a composition that includes diamond particles, enabling them to grind and polish surfaces with precision. Their primary advantages include:
- Exceptional hardness, making them suitable for tough materials like concrete and stone.
- Longevity, as they can endure extensive usage without significant wear.
- Versatility, applicable in various scenarios from floor finishing to repairing automotive parts.
These pads are especially useful when fine finishes are desired. They range in grit sizes, allowing users to achieve different levels of polish, which is critical in both woodworking and automotive applications.
Alumina Oxide Pads
Alumina oxide pads offer a cost-effective alternative to diamond pads, particularly for less demanding applications. Made from processed aluminum oxide, they are commonly used for woodworking projects. They provide several key benefits:
- Function well for initial sanding and surface preparation.
- Available in a wide range of grits to accommodate various needs.
- Generally more affordable than diamond pads, making them accessible for hobbyists and DIY enthusiasts.
While they may not last as long as diamond pads, their performance in sanding and surface finishing tasks makes them a popular choice among woodworkers.
Silicon Carbide Pads
Silicon carbide pads are characterized by their sharpness and ability to cut through hard materials. They are effective for finishing tasks that require a fine touch. Key features include:
- High cutting efficiency, which allows for quicker processing times.
- Effective on tough materials, such as glass and ceramics.
- Good for both wet and dry applications, offering flexibility in use.
These pads tend to wear out more quickly than diamond or alumina options; however, they achieve excellent results in specific contexts, making them valuable to tradespeople and craftspeople alike. Understanding the unique properties of these resurfacing pads can help in making informed choices tailored to specific projects.
Criteria for Selecting Resurfacing Pads
Selecting the right resurfacing pad is vital to achieving the desired outcome in various applications. The efficiency and longevity of a project can hinge on the choice of pad. Understanding the criteria for selecting resurfacing pads helps ensure that users maximize the performance and longevity of their tools. Key elements to consider include material durability, grit size, and compatibility with tools. Each of these aspects contributes to the overall effectiveness and user experience.
Material Durability
Durability is perhaps the most critical aspect when choosing resurfacing pads. These pads undergo significant wear during use, so selecting materials that withstand abrasive conditions is essential. For example, diamond resurfacing pads offer excellent durability, allowing them to last longer against tough surfaces. On the other hand, alumina oxide pads are suitable for moderate applications but might not endure as long under heavy use. Users are encouraged to analyze the working environment and project requirements. For instance, if working with harder surfaces, investing in more durable pads may lead to a better outcome.
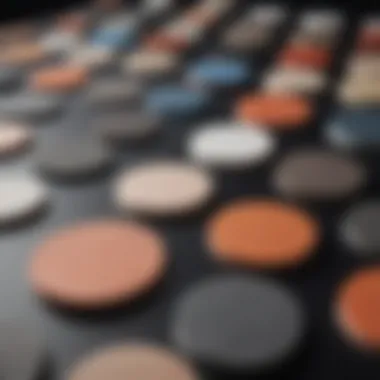
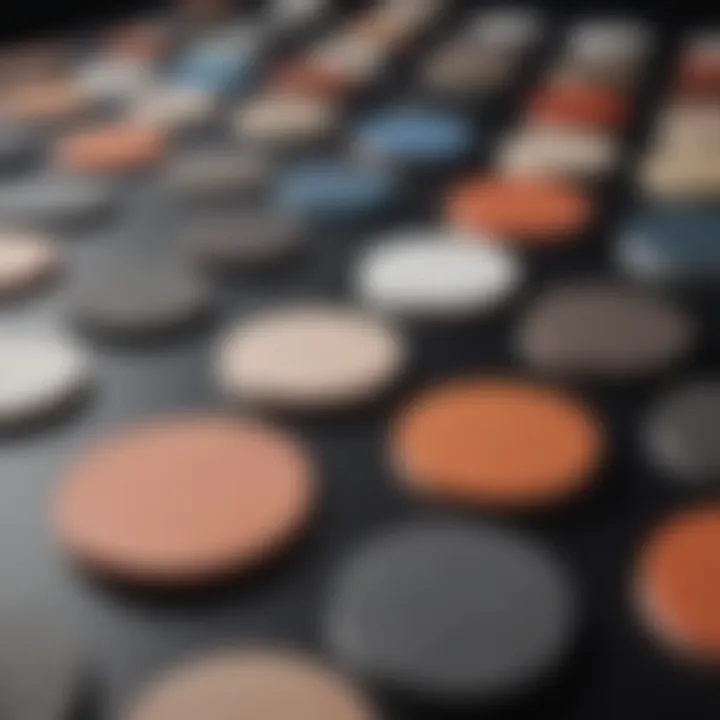
- Hardness: The hardness rating of a material can betray its durability. Harder materials typically offer better longevity.
- Coating: Some pads come with specialized coatings that add an extra layer of protection.
Understanding these factors ensures users make an informed decision that balances performance and cost.
Grit Size Considerations
The grit size of resurfacing pads significantly affects results. Finer grits provide a smoother finish, while coarser grits are better for heavy material removal. Determining the appropriate grit size requires understanding the projectโs needs. For instance, automotive repair might require a coarse grit for roughing surfaces, followed by finer grits for finishing. Conversely, woodworking might demand various grit sizes throughout the process to achieve the desired surface quality.
Common grit sizes and their uses include:
- Coarse (40-80 grit): Used for material removal and initial shaping.
- Medium (80-120 grit): Ideal for smoothing surfaces after heavy work.
- Fine (120-220 grit): Perfect for achieving a polished or finished look.
- Extra Fine (220+ grit): Best for ultra-smooth finishes, often in woodworking or finishes.
Being strategic about grit selection can enhance both efficiency and quality of the end product.
Compatibility with Tools
Compatibility between resurfacing pads and the tools used is another significant factor. Different tools may utilize various pad types or attachment methods. Standardizing tools and pads within your toolkit ensures seamless transitions between tasks and minimizes frustrations. For example, certain power tools, like the Makita 9237CX3, offer a unique attachment design that may not work with all pads.
To enhance the user experience, consider the following:
- Attachment method: Ensure that the pads fit the tool exactly, whether using hook-and-loop, clips, or screws.
- Tool specifications: Refer to the tool manufacturerโs guidelines to find compatible pad sizes and types.
- Versatility: Opt for pads that can be used across multiple tools to reduce costs and increase flexibility.
Applications in Automotive Resurfacing
In the realm of automotive repairs, resurfacing pads play a critical role that cannot be overlooked. These pads enhance the performance and longevity of various automotive components. By using resurfacing pads effectively, mechanics and DIY enthusiasts can ensure that vehicle parts return to optimal working conditions. This section dives into two main applications of resurfacing pads within the automotive sector: brake disc resurfacing and body panel repairs. Each application presents unique benefits and considerations.
Brake Disc Resurfacing
Brake disc resurfacing is a vital process that ensures safe and effective braking performance. When brake discs wear down unevenly, they can cause vibrations and reduce the braking efficiency of the vehicle. Resurfacing pads provide a precise method to smooth out the surface, allowing for better contact with brake pads, which leads to more consistent braking.
The process typically involves removing the brake discs and using specialized resurfacing tools fitted with appropriate pads. Proper selection of the resurfacing pad is crucial. Using pads designed for brake applications ensures minimal risk of damage to the discs and achieves a superior finish. The following points highlight the significance of using resurfacing pads for brake discs:
- Consistency: Ensures a smooth finish for improved contact with brake pads.
- Safety: Reduces vibrations and brake noise, promoting a safer driving experience.
- Cost-Effectiveness: Resurfacing can extend the life of the brake discs, delaying the need for replacements.
"Properly resurfacing brake discs not only improves performance but also enhances vehicle safety."
Body Panel Repairs
Resurfacing pads are also essential for body panel repairs in automotive settings. They are commonly used in the preparation of surfaces for paint or other finishes. When a vehicle sustains damage, the body panels may become uneven or scratched. Using resurfacing pads helps refine the surface before repainting or applying protective coatings.
Different types of pads can be used based on the extent of the damage and the desired finish. For instance, coarser pads may be suitable for deeper scratches, while finer pads are ideal for achieving a smooth surface before applying paint. Here are some considerations for using resurfacing pads in body panel repairs:
- Surface Preparation: Ensures that surfaces are adequately prepared, allowing for better paint adhesion.
- Aesthetic Appeal: Provides a smooth finish that enhances the visual quality of the repair.
- Time Efficiency: Quickens the repair process, leading to faster turnaround times for vehicle restorations.
In summary, resurfacing pads are indispensable tools in automotive resurfacing applications. From brake discs ensuring safety to body panels enhancing appearance, their role cannot be understated. By focusing on the right pads and techniques, automotive professionals can significantly improve repair outcomes.
Woodworking and Resurfacing Pads
In woodworking, resurfacing pads play a vital role in achieving quality finishes and maintaining the integrity of wooden surfaces. They are essential tools that assist in the surface preparation and finishing processes. Proper selection and use of these pads help to enhance the appearance and longevity of wood products.
Understanding the importance of resurfacing pads in woodworking requires recognizing their benefits. They enable smoother finishes, remove imperfections, and prepare surfaces for additional coatings. Additionally, the right pad can extend the life of woodworking tools by lessening wear and tear during the sanding and preparation stages.
Several considerations impact the choice of resurfacing pads for woodworking. Factors such as wood type, desired finish, and project requirements should influence selection. With the correct pad, woodworkers can achieve superior results, thus elevating their craft.
Surface Preparation
Surface preparation is the foundation of any woodworking project. Resurfacing pads help create a clean and smooth surface, which is essential for adhesion of paints, stains, or sealers. Before applying any finish, it is crucial to ensure the wood is free from dirt, dust, and imperfections. Using the appropriate resurfacing pad allows for consistent sanding, making it easier to achieve a uniform surface.
When preparing surfaces, consider the grit size of the resurfacing pads. Coarse grits, such as 60 or 80, are effective for removing roughness, while medium grits, like 120 or 150, are suitable for smoothing surfaces. Final sanding should be done with finer grits, such as 220, to produce a polished finish ready for staining or painting.
Moreover, the technique used during sanding is equally important. It is advisable to follow the wood grain to avoid scratches and achieve finer results. Using consistent pressure is essential as well; too much pressure can damage wood fibers, while too little may not achieve the desired result.
"Proper surface preparation saves time and resources by eliminating the need for excessive finishing and corrections."
Finishing Techniques
Finishing techniques in woodworking do not just enhance aesthetics; they protect wood from damage. The choice of resurfacing pad during this stage is equally important. Different finishes may require specific pads depending on their texture and the desired final sheen.
For example, when working with oil-based finishes, a sanding pad that removes less material while providing a polished look is preferred. In contrast, water-based finishes may benefit from pads designed to enhance adhesion and smooth application. Understanding the finish to be used is key to selecting the correct pad.
The application technique also varies by finish. For varnishes and lacquers, a soft-touch application is recommended to avoid roller marks. If you are using a brush, ensure that you choose pads that allow for easy maneuvering, especially in intricate areas.
Integrating resurfacing pads into finishing techniques not only supports the desired look but also prolongs the life of the wood. The finish protects against moisture, UV light, and everyday wear, ensuring the project remains attractive and functional for years to come.
Overall, proper use of resurfacing pads in both surface preparation and finishing techniques in woodworking is essential. It lays the groundwork for quality, durability, and satisfaction with the final product.
Construction Applications
The role of resurfacing pads in construction cannot be understated. These tools are integral in various tasks such as floor leveling and tile preparation. The construction industry often demands precision, durability, and efficiency. Selecting appropriate resurfacing pads can significantly impact the quality of the finished work. Understanding the specific functions and advantages of these pads is crucial for professionals in this field.
Floor Leveling
Floor leveling is an essential aspect of construction that ensures surfaces are even and suitable for further work. Resurfacing pads designed for this application are typically made from durable materials that can withstand heavy usage. They are intended to smooth and perfect concrete and other floor surfaces, preparing them for finishing. Without proper leveling, subsequent work like laying flooring could be compromised, leading to longer project timelines and increased costs.
When using resurfacing pads for floor leveling, consider the grit size. A coarser grit will remove material more rapidly but may not provide the smooth finish needed for later applications. Conversely, finer grits are better suited for finishing touches but might require more passes to effectively level a surface.
Best Practices for Floor Leveling:
- Assess the Surface: Always check the condition of the surface to be leveled. This helps in selecting the right pad.
- Start with Coarse Grit: Begin with a coarser pad to remove excess material.
- Finish with Fine Grit: Switch to finer pads for a smooth finish.
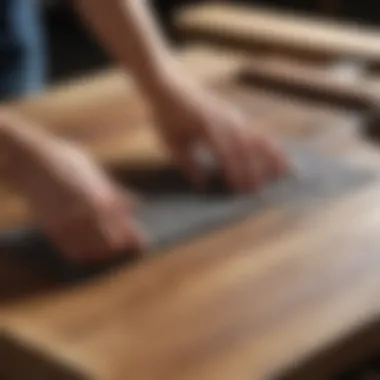
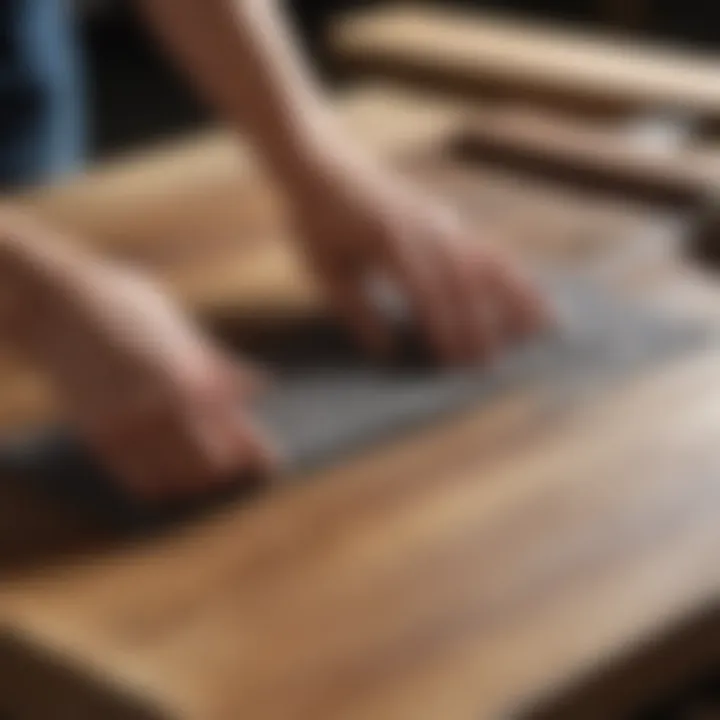
Tile Preparation
Tile preparation is another critical use of resurfacing pads in construction. This stage is vital because proper preparation ensures that tiles adhere effectively and maintain durability over time. Resurfacing pads can help eliminate imperfections from existing surfaces, making them ready for tile installation. This can involve removing old adhesive or smoothing out rough patches.
When preparing a surface for tile, it is essential to use pads that are compatible with both the substrate and the tiles themselves. Different materials may require unique surface finishes, so understanding the needs of the specific tiles can guide the choice of resurfacing pad.
Key Considerations for Tile Preparation:
- Surface Condition: Inspect the area thoroughly for any damage or irregularities.
- Material Compatibility: Ensure that the resurfacing pad is suitable for the underlying material.
- Uniformity: Achieve a consistent surface quality, free of dust and debris that could impact adhesion.
In summary, effective resurfacing pad usage in construction applications aids in achieving professional results. Investing in quality pads specifically designed for floor leveling and tile preparation provides a foundation for successful installation and finishing processes. Engaging in thorough preparatory work can save both time and resources down the line.
Best Practices for Using Resurfacing Pads
Employing proper techniques when using resurfacing pads is essential for achieving optimal results in various applications. Effective usage reflects not only on the work quality but also influences the durability of the pads themselves, thereby ensuring they remain effective over time. Understanding these best practices can significantly enhance both user experience and output quality.
Proper Handling Techniques
Handling resurfacing pads correctly is one of the fundamental aspects of their successful use. Users must ensure they hold the pads with a steady grip, allowing for precise movement during application. Always check that the pads are secure on the equipment to avoid slippage or accidental detachment, which may lead to uneven surfaces or damage. When storing the pads, avoid using excessive weight on top of them, as this can warp or damage their structure. It is prudent to routinely inspect pads for any wear or damage before use. If irregularities are noticed, replace them to maintain high performance.
Optimal Pressure Application
The pressure applied during resurfacing is critical for effectiveness. Users should apply just enough pressure to achieve the desired surface alteration without forcing the tool against the material too hard. Excessive pressure can lead to overheating, causing the pads to wear out rapidly or even fail altogether. To gauge appropriate pressure, it helps to start with light pressure and gradually increase until optimal results are observed. Keep in mind that different materials may require varying levels of pressure, so adapting to the specific project is necessary for maintaining control and precision.
Maintaining a Steady Speed
Consistency in speed during the resurfacing process is vital. Moving too quickly can result in uneven surfaces, while moving too slowly may lead to unnecessary pad wear. It is advisable to find a rhythm that allows for even coverage without excessive pressure or heat buildup. Practicing different speeds on spare materials can aid in developing a feel for the necessary pace. This practice will enable users to confidently approach their projects, ensuring that they achieve desirable finishes without compromising the resurfacing pads' integrity.
Key Point: Following these practices ensures not merely the longevity of the resurfacing pads but also the quality of the work, reducing the need for re-work.
Overall, these best practices represent a framework that can help all users enhance their efficiency and effectiveness in various applications involving resurfacing pads.
Maintenance of Resurfacing Pads
Maintaining resurfacing pads is crucial for their longevity and effectiveness. Proper maintenance ensures that these tools continue to perform at optimal levels, minimizing the risk of damage to the surfaces being worked on. When you invest in resurfacing pads, regular upkeep can save costs and prevent the inconvenience of frequent replacements.
Cleaning Procedures
Cleaning resurfacing pads should be approached systematically. After every use, it is beneficial to remove debris and dust that accumulate on the surface. Most resurfacing pads can be cleaned by simply rinsing them with water to clear off material residue. Depending on the material, using a soft brush can help dislodge stubborn particles. Here are some key steps for effective cleaning:
- Rinse with Water: Use lukewarm water to wash off residue. Cold water could be less effective in some cases, especially with tough grime.
- Brush Gently: Utilize a soft-bristled brush to sweep away fine particles without damaging the pad.
- Dry Completely: Ensuring that the pads are completely dry before storage prevents mildew and other damages.
Storage Recommendations
Proper storage is another element that significantly affects the life of resurfacing pads. When these pads are not in use, they should be stored in a cool, dry place, away from excess heat or moisture. Safeguarding pads from extreme conditions keeps their structure intact and ready for the next application. Some practical storage tips include:
- Use a Dedicated Container: Keep your pads in a dedicated box or bag that is clean and free from sharp objects that could scratch their surfaces.
- Stack Carefully: Store pads flat or in stacks to prevent warping. Ensure they are not under heavy items that might change their shape.
- Labeling: If you have various pads, consider labeling them for easy identification, which can save time.
These maintenance practices are vital for maximizing the performance and lifespan of resurfacing pads. As you follow these guidelines, you will find that well-maintained pads lead to better results in your projects.
Cost Analysis of Resurfacing Pads
Understanding the cost dynamics of resurfacing pads is essential for both professionals and DIY enthusiasts. This section delves into budget considerations, and the relationship between cost and quality, providing a comprehensive perspective on managing expenses while ensuring effective project outcomes. Cost analysis helps users to identify not only where money can be saved but also the importance of investing in quality materials to avoid poor results in the long term.
Budget Considerations
When planning any project, budgeting is crucial. Resurfacing pads can vary widely in price based on the material, brand, and grit size.
- Quality vs. Price: It might be tempting to go for the cheapest option available, but consider that lower-priced products may not last as long or perform as well. In some cases, paying slightly more initially can lead to savings in the long run through enhanced durability and efficiency.
- Bulk Purchasing: Often, retailers offer discounts for bulk purchases. If the project requires a considerable quantity, buying in bulk could be a good strategy to lower the overall cost.
- Tool Compatibility: Ensure that the selected pads are compatible with your tools. Using pads that do not fit well can result in inefficiencies and additional costs for replacements or additional tools.
It's prudent to allocate a specific percentage of your project budget to resurfacing pads. This ensures you have adequate funds for quality materials without compromising other areas of your project.
Cost versus Quality Analysis
In many instances, the adage "you get what you pay for" rings true in the realm of resurfacing pads. Analyzing the balance between cost and quality is vital in making informed purchasing decisions.
- Performance: Higher quality pads generally deliver superior performance. They are designed for specific tasks and can improve the finish of the surface significantly.
- Durability: Cheaper pads might wear out quickly, leading to frequent replacements. Investing in quality pads will often yield better results and fewer replacements, eventually saving costs.
- Brand Reputation: Consider established brands like Norton or 3M, known for their quality. These brands may charge more but often offer extensive warranties and customer support, which can be beneficial in the long run.
Ultimately, consistently high-quality resurfacing pads can yield better results, reduce the need for rework, and support a smooth project experience. Finding the right balance between cost and quality requires careful evaluation of all options available in the market.
"When you invest in quality, you invest in the longevity and efficiency of your projects."
By understanding these factors, users can make choices that align with their budgets while achieving optimal results.
Innovations in Resurfacing Technology
In recent years, advancements in resurfacing technology have transformed the landscape of several industries, including automotive, woodworking, and construction. These innovations not only enhance the functionality and durability of resurfacing pads but also improve efficiency and user experience. Understanding these developments is crucial for selecting the right resurfacing pads tailored to specific applications and ensuring optimal results.
Emerging Materials
New materials are at the forefront of innovations in resurfacing pads. Manufacturers are now experimenting with composites that combine the best features of traditional materials like diamond, alumina oxide, and silicon carbide. For instance, the introduction of ceramic-based pads offers several advantages:
- Increased Durability: Ceramic pads tend to last longer due to their hardness and resistance to wear.
- Fine Finish: They provide smoother finishes, which is particularly beneficial in woodworking applications.
- Versatility: Applicability extends across various surfaces, such as metal and composite materials.
Using these emerging materials allows practitioners to achieve superior results in less time. When selecting resurfacing pads, itโs essential to consider the type of material being used and how it aligns with the desired finish and durability requirements.
Smart Technology Integration
The integration of smart technology into resurfacing tools has also made significant strides. Equipment fitted with smart features offers real-time data about the conditions of the pads and surfaces, providing several benefits:
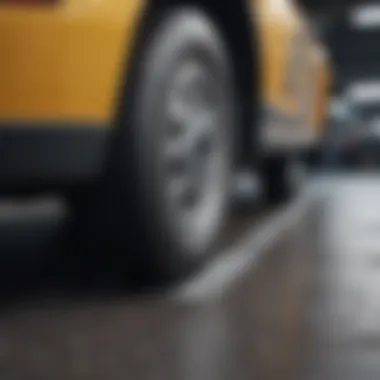
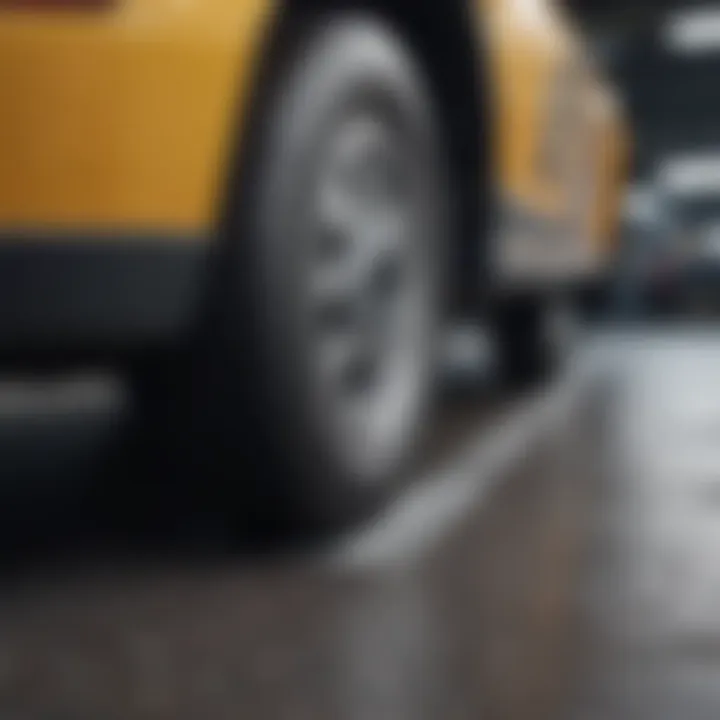
- Performance Tracking: Users can monitor the wear and performance of pads in real time, allowing for timely replacements.
- Automated Settings: Some machines can adjust speed and pressure based on the material being worked on, enhancing efficiency.
- User Safety: Smart technology can include safety features like automatic shut-off if excessive heat or pressure is detected.
These innovations not only enhance the quality of resurfacing work but also promote safe practices. Investing in smart technology can ultimately lead to better project outcomes while minimizing the risk of errors or accidents.
"Incorporating technology into resurfacing processes can dramatically elevate the quality of work while ensuring safety and efficiency."
In summary, innovations in resurfacing technology, particularly emerging materials and smart technology integration, hold the potential to significantly impact how resurfacing projects are approached. Adapting to these changes can lead to improved results in various applications.
Environmental Considerations
Environmental considerations are essential in any industry today. With increasing awareness of ecological issues, it becomes vital to assess how resurfacing pads impact the environment. Isolation of specific elements in the manufacturing and disposal processes is crucial. Decisions made about resurfacing pads can influence not only the efficiency of projects but also the planet's health.
Sustainability in Manufacturing
Sustainable manufacturing practices are increasingly becoming a standard in producing resurfacing pads. Utilizing materials that are less harmful to the environment is a step forward. Manufacturers are integrating recycled or eco-friendly components into their products. This approach reduces the carbon footprint associated with production. The use of sustainable practices often leads to reduced waste and lower energy consumption.
The benefits of sustainable manufacturing extend beyond environmental aspects. Companies adopting these practices can see improvements in their brand image. Many consumers prefer purchasing products that align with their values. For resurfacing pads, manufacturers can highlight their commitment to sustainability as a key selling point.
Recycling Used Pads
Recycling used resurfacing pads is another critical aspect of environmental considerations. After their useful life, pads worn from various applications should not simply end up in landfills. Recycling provides an opportunity to reclaim materials and reduce waste.
There are processes available for the recycling of these pads. For instance, some facilities can turn old pads into raw materials for new products. Others might help repurpose them for different applications. Here are several points to consider about recycling used pads:
- Reduced Waste: Recycling minimizes the amount of material sent to waste disposal.
- Resource Conservation: By reusing materials, the need for new resource extraction decreases.
- Lower Carbon Emissions: Recycling processes typically consume less energy than creating new products.
Encouraging the recycling of resurfacing pads can foster a culture of sustainability. As awareness grows, more consumers and businesses are likely to seek eco-friendly options.
"Sustainable choices in construction and automotive sectors can lead to significant long-term environmental benefits."
By prioritizing environmental considerations, such as sustainable manufacturing and effective recycling methods, there is potential not only for ecological benefits but also for innovations in resurfacing pad technologies.
Safety Precautions
In any project involving resurfacing pads, safety measures are crucial. Proper precautions help minimize risks associated with dust inhalation, noise exposure, and the physical demands of the work itself. Understanding the significance of these safety precautions ensures that users operate effectively while protecting themselves from potential hazards.
When working with resurfacing pads, the environment can become hazardous due to flying debris, chemical exposure, or excessive noise. Thus, knowing how to safeguard oneself is essential for every userโwhether novice or expert.
Personal Protective Equipment
Personal protective equipment (PPE) is a fundamental aspect of ensuring safety during resurfacing tasks. This equipment should be selected according to the specific type of work and the materials involved. Here are key items that should be considered:
- Safety Goggles: Protects the eyes from flying particles and dust.
- Respirators: Important for inhaling quality air in dusty or chemically treated environments.
- Hearing Protection: Use earplugs or earmuffs to limit exposure to loud machinery.
- Gloves: Preserves hands from abrasions or chemicals during the application process.
- Dust Masks: To reduce inhalation of fine dust created during resurfacing.
Proper use of PPE not only provides a barrier against risks but also promotes a safer work environment. It is advisable to conduct regular checks on the effectiveness and integrity of PPE. Additionally, users should be trained on how to wear and maintain their equipment adequately.
Risk Assessment Measures
Conducting a risk assessment is an invaluable part of project planning when using resurfacing pads. This process involves identifying possible hazards and determining how to mitigate them effectively. Here are steps to consider:
- Inspection of Work Area: Ensure that the work environment is clean and free from obstacles that could cause accidents.
- Material Handling: Understand the characteristics of the materials being used. Some may pose risks like toxicity or flammability.
- Equipment Checks: Before commencing work, inspect tools and machines for any defects or malfunctions.
- Training and Awareness: Ensure that all operators have appropriate training on the correct usage of resurfacing pads and their equipment.
- Emergency Procedures: Establish clear emergency protocols in the case of accidents, including first aid and evacuation plans.
By implementing robust risk assessment measures, users can significantly reduce the chance of accidents, ensuring a safer working environment. It creates a proactive framework for identifying dangers and establishing useful protocols in response.
Compliance with safety measures can ultimately lead to higher productivity and confidence among users.
In summary, emphasizing safety precautions in resurfacing pad applications helps in recognizing hazards, wearing appropriate personal protective equipment, and conducting thorough risk assessments. These steps are vital in ensuring a safe and efficient working environment.
User Reviews and Recommendations
User reviews and recommendations play a critical role in the selection process of resurfacing pads. Consumers often look to the experiences of others to determine the effectiveness and reliability of these tools before making a purchase. Reviews provide insights that manufacturers often do not disclose, such as long-term durability, ease of use, and performance under specific conditions. By examining opinions from fellow users, buyers can better understand which products are best suited for their unique needs.
User feedback also highlights common issues or advantages that may not be immediately apparent. For example, a pad that seems perfect may actually have a flaw, like excessive wear when used on certain surfaces. This collective information assists prospective buyers in making an informed decision, enhancing their likelihood of a successful outcome in projects.
Top-Rated Brands
In the resurfacing pad market, several brands consistently receive high marks from users. These brands often prioritize quality, innovation, and user satisfaction. Recognizable names include 3M and Norton. Each offers a range of options tailored to different applications, whether it's automotive, woodworking, or flooring.
- 3M: Known for its advanced materials and significant research efforts, 3M's pads are often highlighted for their longevity and efficiency.
- Norton: This brand provides a diverse selection of high-performing resurfacing pads suitable for various applications, thus appealing to a broad audience.
- Makita: Offers competitively priced options that deliver good results for DIY enthusiasts.
These brands often receive repeated endorsements from users who appreciate their durability and effective results.
Frequently Recommended Models
Apart from brands, specific models of resurfacing pads frequently emerge in user discussions as top picks. Each model's unique characteristics cater to different user needs, ensuring optimal performance in various applications.
- 3M Cubitron II: Highly regarded for its cutting efficiency and durability, this model is perfect for heavy-duty applications.
- Norton BlueFire: Known for itโs versatility, this pad is recommended for both professional and DIY projects, making it a popular choice among users.
- Makita 7-Inch Diamond Pad: Many users recommend this model for its ability to tackle surface blemishes effectively.
Regularly engaging with user reviews enables buyers to narrow down choices based on actual performance rather than marketing claims. As the resurfacing pad landscape continues to evolve, staying informed through consumer feedback becomes ever more essential.
Epilogue
In this article, we have explored the multifaceted world of resurfacing pads, emphasizing their vital role across various industries, including automotive, woodworking, and construction. Understanding how to select, apply, and maintain these pads is crucial for achieving optimal results in any project. The insights provided here can lead to enhanced efficiency, allowing users to maximize the effectiveness of their tools.
Key Takeaways
- Know Your Materials: Different types of resurfacing pads serve unique purposes. For instance, diamond pads offer durability, while aluminum oxide pads can be more cost-effective. Understanding the material is essential for selection.
- Correct Usage Techniques: Using the right handling methods and applying proper pressure can significantly influence the results. Maintaining a steady speed while working also minimizes tool wear.
- Regular Maintenance: Cleaning and storing pads appropriately extends their lifespan. Implementing maintenance routines ensures consistent performance and reduces costs over time.
- Safety First: Utilize personal protective equipment to safeguard against potential hazards. Risk assessment helps identify and mitigate dangers during operation.
Future Trends
Resurfacing technology continues to evolve, highlighting several trends that may shape its future:
- Innovative Material Development: Research into new materials is ongoing. Emerging compounds may offer better durability and performance than traditional options.
- Integration with Smart Technology: As technology advances, integrating smart sensors into resurfacing tools becomes a possibility. Such technology can monitor usage patterns and maintenance schedules, ensuring optimal tool lifespan.
- Sustainable Manufacturing Practices: The push for sustainability is likely to influence how resurfacing pads are manufactured. Expect to see increased use of recycled materials and eco-friendly processes.
By staying informed about these trends, users can adapt to changes in the industry. Such preparedness will allow for better decisions on tools, ultimately leading to more successful projects.